Typical Challenges in Welding Inspection Madison and How to Overcome Them
Typical Challenges in Welding Inspection Madison and How to Overcome Them
Blog Article
The Relevance of Thorough Welding Examination in Industrial Applications
In the realm of industrial applications, the relevance of thorough welding inspection can not be overemphasized. As we discover the multifaceted benefits of thorough welding inspections, one should consider the wider ramifications on security, reliability, and cost-effectiveness in industrial operations.
Enhancing Architectural Honesty
When it comes to welding examination in industrial applications, boosting structural stability is vital. The key objective of welding assessment is to make certain that the welds are capable of bearing the expected lots and stress and anxieties they will encounter in service. This involves an extensive analysis of the welds' dimensions, placement, and total top quality, ensuring they satisfy the specified codes and standards. Exact examination techniques, such as aesthetic assessment, ultrasonic testing, and radiographic screening, are vital in determining concerns that could endanger the framework's safety and functionality - Welding Inspection Madison.
The importance of maintaining architectural honesty in bonded frameworks can not be overstated. Improperly executed welds can bring about catastrophic failures, resulting in pricey fixings, downtime, and even endangerment of human lives. Examiners play a crucial role in the lifecycle of industrial elements, providing guarantee that the welding procedure supplies the desired stamina and sturdiness.
Additionally, progressed technologies, such as phased array ultrasonic screening and digital radiography, offer boosted capabilities in finding possible weaknesses, permitting for restorative procedures prior to problems intensify. By focusing on the stability of welds with meticulous inspection, industries can guarantee functional efficiency and prolong the durability of their framework.
Determining Welding Issues
Identifying welding issues is a vital aspect of ensuring the security and dependability of welded frameworks. These issues can compromise the integrity of the entire assembly and, if left unaddressed, might result in tragic failures. Common welding defects include porosity, cracks, insufficient fusion, and damaging. Each of these problems develops from details reasons, such as improper welding methods, contamination, or inadequate heat control.
Knowledgeable examiners make use of both aesthetic evaluation and advanced non-destructive testing (NDT) techniques, such as radiographic or ultrasonic testing, to find these defects. The prompt recognition and correction of welding flaws are vital to maintain the architectural honesty and durability of industrial elements.
Guaranteeing Compliance Standards
Preserving the honesty of welded structures expands past determining issues; it requires adherence to strict conformity requirements. Conformity with well established requirements, such as those provided by the American Welding Society (AWS) and the International Company for Standardization (ISO), ensures that welds meet minimal safety and quality needs. These requirements encompass a variety of criteria, including product specifications, welding treatments, and certification of welders. Adherence to these requirements is important to stop structural failings, which could bring about catastrophic consequences in industrial applications.
Routine audits and evaluations are crucial in verifying conformity. Examiners have to have a thorough understanding of the pertinent requirements and be experienced at utilizing various non-destructive website here testing (NDT) techniques to examine weld high quality. By guaranteeing that welding practices line up with conformity requirements, companies alleviate the threat of non-conformity, which can bring about legal responsibilities and security hazards.
Additionally, preserving conformity not just safeguards structural stability yet likewise boosts a business's credibility in the sector. Stakeholders and customers are most likely to trust companies that continually show a commitment to top quality and security through rigorous conformity. Hence, making sure compliance requirements is a critical part in the effective implementation of welding in commercial applications.
Reducing Upkeep Expenses
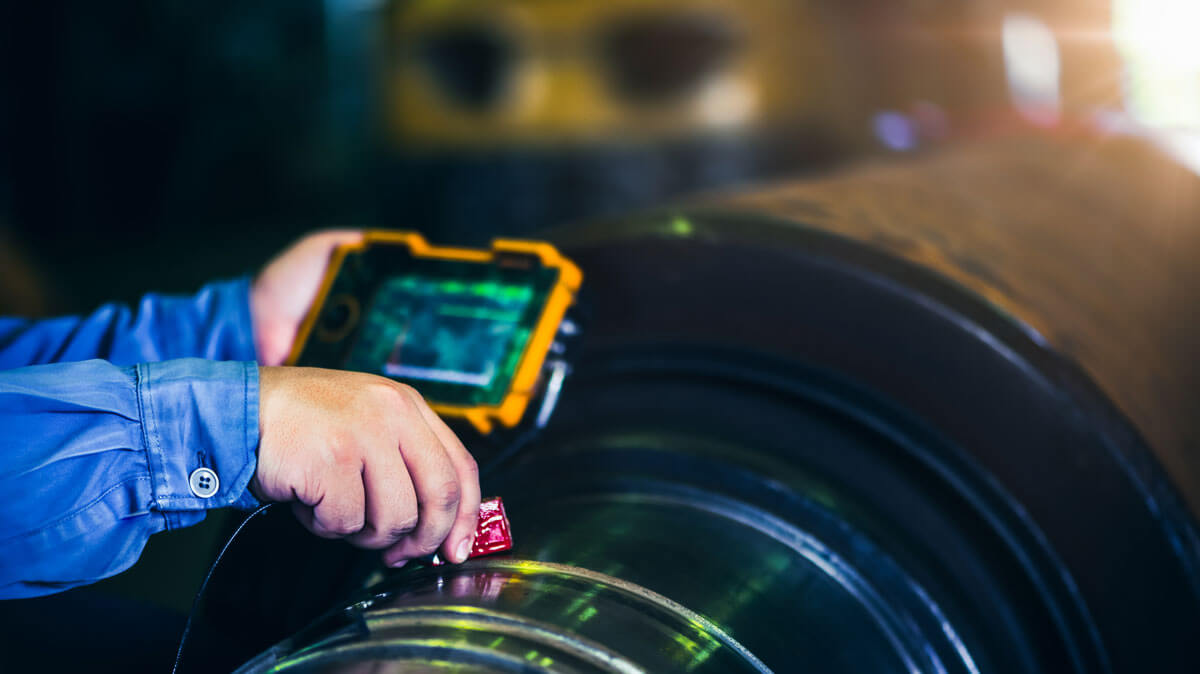
The application of advanced non-destructive testing (NDT) techniques, including ultrasonic, radiographic, and magnetic bit evaluations, enhances the capacity to identify subsurface problems without endangering the architectural stability of elements. By utilizing these techniques, industries can dramatically prolong the life span of their tools, reducing downtime and the connected monetary burden of maintenance activities.
In addition, a robust welding evaluation program sustains the optimization of upkeep routines, moving from reactive to predictive maintenance techniques. This proactive strategy not just reduces unanticipated failures yet also improves source allowance, guaranteeing that upkeep efforts are focused and reliable. Inevitably, try this out the financial investment in extensive welding evaluation is balanced out by the significant financial savings realized with lowered maintenance demands, contributing positively to the overall operational effectiveness of industrial enterprises.
Improving Precaution
Welding inspection plays an important function in this context, as it guarantees that all connections and joints satisfy rigorous safety and security criteria. Comprehensive inspections assist identify defects such as splits, porosity, or insufficient fusion that can endanger structural honesty.
To enhance safety and security actions, embracing sophisticated non-destructive testing (NDT) methods is essential. Methods like ultrasonic screening, radiographic testing, and magnetic particle assessment allow for detailed assessment without harming the framework. These innovations allow inspectors to detect concealed defects early in the construction process, facilitating timely corrective activities. Implementing a robust high quality control system that consists of routine training for examiners and welders guarantees adherence to developed safety requirements.
Finally, promoting a culture of safety and security within the company stresses the relevance of detailed welding inspections. Encouraging open interaction and collaboration amongst welders, designers, and inspectors adds to a shared dedication to safety and security quality. Welding Inspection Madison. In doing so, industries can protect their procedures, safeguard employees, and keep public trust fund

Final Thought
Thorough welding evaluation is indispensable in commercial applications, substantially improving architectural honesty and integrity. Inevitably, the attentive implementation of welding assessments plays an essential role in keeping operational efficiency and safety in industrial setups.
As we click here to find out more discover the diverse benefits of diligent welding inspections, one must think about the wider ramifications on safety, dependability, and cost-effectiveness in industrial procedures.
The primary goal of welding assessment is to ensure that the welds are qualified of bearing the anticipated anxieties and loads they will encounter in solution. Efficient welding examination plays an essential duty in decreasing these costs by guaranteeing the stability and longevity of welds, thereby alleviating the threat of early failings.Complete welding assessment is crucial in commercial applications, significantly boosting structural integrity and reliability. Eventually, the diligent execution of welding examinations plays a vital role in preserving operational efficiency and safety and security in commercial settings.
Report this page